By Anna Ringstrom
STOCKHOLM (Reuters) – Nordic pulp makers are developing clean ways to turn birch and pine trees into clothes or sofa covers to help revive their industry and meet demand from fashion and furniture firms for alternative textiles to cotton.
There has been no Nordic production of viscose, the main textile fiber from timber, since the last manufacturer stopped nearly a decade ago, partly on environmental grounds.
But a 2011 spike in cotton prices contributed to increased global demand for viscose and lyocell, the other major textile fiber from wood pulp. Production is dominated by Austria’s Lenzing, India’s Aditya Birla and South Africa’s Sateri.
Three Nordic mills export dissolving pulp, the product that can be turned into textile fiber. The industry would like to see textile fiber factories set up at home that will meet environmental rules and appeal to local firms such as IKEA and Hennes & Mauritz which want to project a green image.
“We have the forest here in the Nordics, we have our pulp mills. It would be better for us if more dissolving pulp was needed in our region,” said Markus Mannstrom, chief technical officer of Finland’s Stora Enso The forestry industry, which accounts for a fifth of Finland’s and a tenth of Sweden’s exports, has been hit by lower newsprint demand and foreign competition. But global output of pulp for textiles is expected to grow 30 percent by 2020 from 4.4 million tonnes in 2015, according to Oliver Lansdell at forest products industry consultancy Hawkins Wright.
Anticipating the rise in demand, in 2011 Sodra, the Swedish association of 50,000 small forest owners, converted a paper pulp machines so they could make textile pulp. Stora Enso did the same in 2012.
Sweden’s Domsjo, which has made dissolving pulp since the 1930’s and was bought by Aditya Birla in 2011, said demand has risen.
“We expect cotton output to peak while textile demand will keep growing,” said Dag Benestad, head of dissolving pulp production at Sodra.
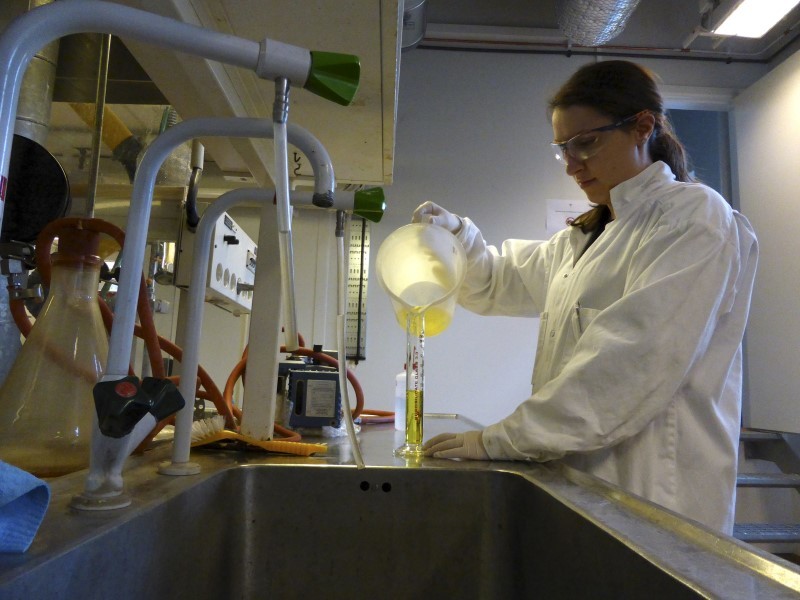
CATCHING UP
The next step would be to set up factories at the mills, creating new jobs and saving money on energy and the cost of transporting for export. Sodra, Domsjo and Stora Enso are among those intensifying research into greener fiber production processes.
Stora Enso in 2015 opened a research center in Stockholm that looks into how to make viscose production less toxic. Domsjo and Sodra are part of a large project looking at how best to integrate a textile factory with a mill so that the chemicals are recycled.
Recycling or replacing chemicals is essential to restarting production of textile fiber from timber in a region where the pulp industry’s image was also tarnished by heavy pollution. It now uses “closed loop” production that stops chemicals seeping out.
Carbon disulfide is the main polluter of viscose production. Swedish Research institute Innventia’s Fredrik Aldaeus, who is fine-tuning a method to make pulp that dissolves more easily with reduced or zero carbon disulfide, said a modified viscose fiber plant could be up and running within five years.
The main alternative textile fiber from timber pulp is lyocell which was first developed in the 1970s and has a cleaner manufacturing method than viscose. It has been marketed by Austria’s Lenzing as Tencel since the 1990s.
Nordic researchers are trying to develop something similar. Herbert Sixta, who used to work at Lenzing, has led development at Aalto and Helsinki universities of a new lyocell-type fiber.
“In three to four years we should be able to show if it’s commercially viable provided that we get the necessary financial support,” he said.
CHEERING THEM ON
H&M and IKEA, both at the forefront globally in their sectors on sustainability, are alongside smaller Nordic fashion brands such as Filippa K, are cheering on and cooperating with the pulpmakers, keen to sell products made using local forests to environmentally-conscious shoppers.
“We want them to find a more sustainable way to produce viscose,” said Cecilia Brannsten, sustainability expert at H&M, which has increased its use of Tencel in recent years because it has a better green profile despite being more expensive.
“Today’s viscose can’t directly be replaced with the more sustainable lyocell because they look and feel different.”
H&M and IKEA said they were providing funding for state- and industry-owned research institute Swerea, which recently launched an industrial-scale test of a new viscose-like process. They declined to say how much they had contributed.
Along with Sodra, they were also part of a consortium that in 2014 shelved a project using cold alkali as solvent amid differing opinions about how to proceed.
“We constantly look for innovations and innovators,” IKEA Group spokeswoman Josefin Thorell said in an email.
“We support the Swerea…project which we believe can contribute to a more sustainable future textile production,” but added that it was too early to say how long it would take to work out if the project was viable.
(Editing by Anna Willard)